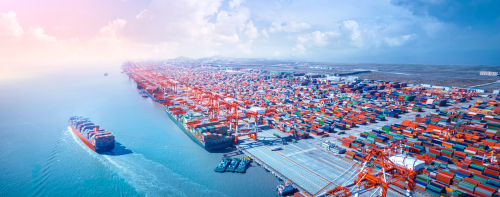
In a Europe already sorely tried by more than two years of pandemic, the crisis born with the war in Ukraine risks being the real coup de grace for some nations.
It is not only the citizens, grappling with inflationary spirals and high utility bills, who are paying the price, but also and above all the productive and entrepreneurial world.
Indeed, the sum of several factors could prove fatal for economies already deeply affected by Covid.
But if the race to contrast energy costs, gas in primis, seems to involve all the main European countries in the search for quick and efficient solutions, the critical situation of the supply chain appears difficult to solve.
Let’s start with an assumption: around 90% of trade takes place by sea, followed by road or rail transport and the entire distribution system that follows.
The sum of the scenarios of recent years has led to dramatic consequences with regard to the functionality and costs of this chain.
From covid 19 onwards, the transport crisis and in particular the shipping container crisis, after a very short lull, was in fact reignited due to the conflict in Ukraine and rising fuel costs.
A container from China, the world’s main route from the port of Shanghai, can now cost over 300% more than in the pre-coastal era, to which must be added an almost threefold increase in cost due to various concomitant causes: the backlog of goods, a shrinking workforce, and increased time and customs controls.
Cargo ship delays have disrupted the supply chains of many companies, with particularly problematic effects for those that use production processes that tend to minimise warehouse stocks by relying on a type of organisation known as ‘just in time’, which involves the procurement of raw materials and semi-finished products exactly when they are needed, like many manufacturers in the automotive market, in order to avoid the costs and risks associated with warehouse storage.
On the export side of finished products, the situation is also particularly critical, with the almost total blocking of foreign sales of some products due to ‘uneconomicity’: the cost of transport far exceeds the cost of the product, which would consequently be overpriced to make it attractive to the buyer.
In Italy, to cite an example, olive oil exports have plummeted due to increased transport costs to two of the main importing countries, Australia and the United States. At the same time, many products are not imported from China for the same reason: excessive transport costs.
A real domino effect is therefore causing a steady increase in prices and inflation.
One of the causes that led to this crisis situation is undoubtedly that of glocalisation policies, which pushed many to produce in China or other countries where costs were lower than in their own country, especially those related to labour, although often to the detriment of the quality of the products themselves. Such delocalisation policies have in fact caused the gradual disappearance of part of the national production capacity.
However, the solution to this critical phase does not seem to be quick and easy.
There is currently a global trend towards a return to regionalisation of supply chains through reshoring, i.e. the relocation of production phases to countries of origin or ‘friendly’ countries and a return to stockpiling and stockpiling policies.
Certainly, it will be difficult to reverse the trend in the short term, not least because of the risk that costs will be higher than expected, but equally certainly a rethinking of the supply chain is required, to make it as unrelated as possible to increasingly unpredictable scenarios such as those that have recently occurred.
As far as Italy is concerned, the cost of labour makes a reallocation of production on national soil seem unfeasible, at least at the moment. At the same time, our commercial ports are certainly not in line with the other main European ones.
We therefore hope that the next government will be able to take charge of this issue, before, as happened with gas, it is too late.
Author: FeMo